Regardless of what you call them; turntables, bull gears, slewing rings, gear, rotation gear, etc., bearings are a critical component and a large expense. Proper installation and maintenance will help ensure you get the longest life out of your bearing. Not only will you see extended life, but regular inspections will make every day rotation smoother, quieter, more efficient, and most importantly, safe for you and/or your crew.
After the initial installation, there are a few critical components to a bearing that must be checked regularly. First is a simple visual inspection of the gear teeth, should you have them, seals, and mounting structure. Next are the mounting bolts for both the inner and outer rings. And lastly, the bearing grease, both inside and out. Here, we cover each step, then give you an idea of when a bearing should be replaced:
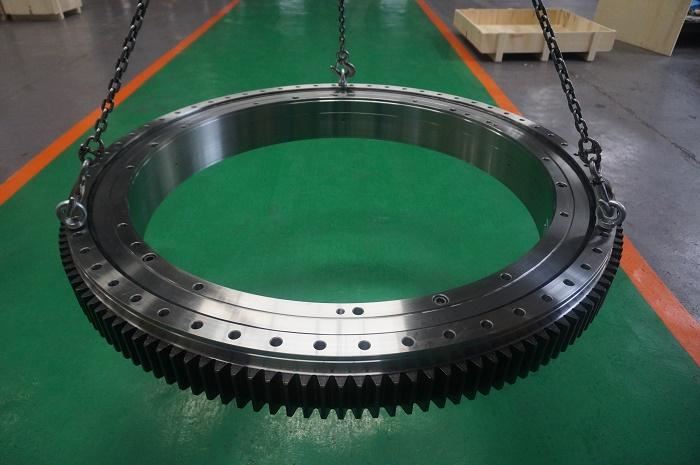
VISUAL INSPECTION:
While you may glance at the bearing every day as you climb into your crane or excavator, we recommend a regular, thorough visual inspection of the bearing and mounting structure. This can help catch small changes well before they turn into bearing-ruining issues, costing thousands. The inspection should include looking for debris in the gear teeth and that teeth are free of cracks or degradation, making sure the seal is intact and correctly seated, all bolts are accounted for and in working condition, and that the mounting structure is free of warping or cracks. We understand this is made more difficult by internally geared bearings or shrouds, but, a simple inspection goes a long way.
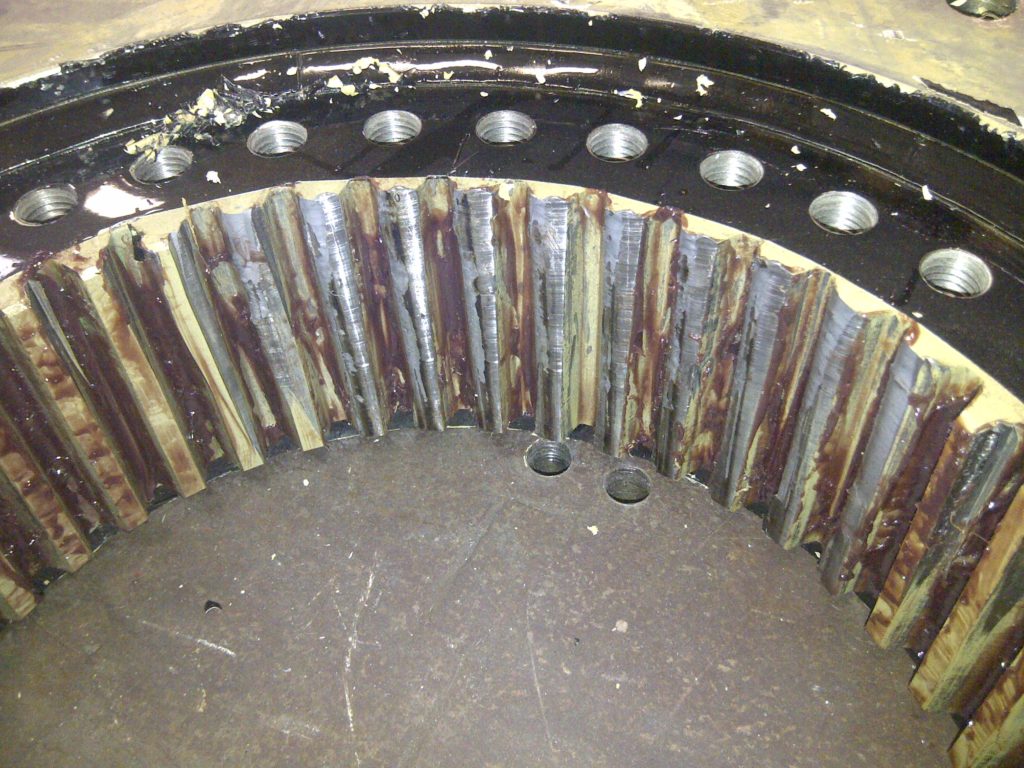
BOLTS:
Through long-term use under load, bolts begin to stretch and will slide and shift if not properly maintained. This shifting, which puts shear loads on the bolt, can wreak havoc on your machine. Worst case, bolts can begin shearing, sending bolt heads throughout the work zone. This shifting also affects the internal workings of the bearing, as load distribution and balancing is altered. Long-term, this can lead to brinelling of the raceway and premature bearing failure.
To avoid these problems, we recommend inspecting and tightening your Grade 8 bolts, or higher, to 70% of yield every 200 hours of use. This timeframe should be shortened if your application sees a lot of vibration, water, or sea air. If upon inspection you notice over 20% of your bolts being noticeably loose (less than 80% of torque), we recommend replacing the bolts, washers, and nuts. When tightening, be it during inspection or initial installation, we recommend using a Star or “Z” pattern. The internal axial clearance of most standard turntable bearings ranges from .05-.15mm, so using the correct pattern is crucial to help avoid any tight spots in rotation.
If you do see sheared bolts, call an expert. It could be any number of issues, including dynamic loading and capacity, bolt quality, or initial installation.
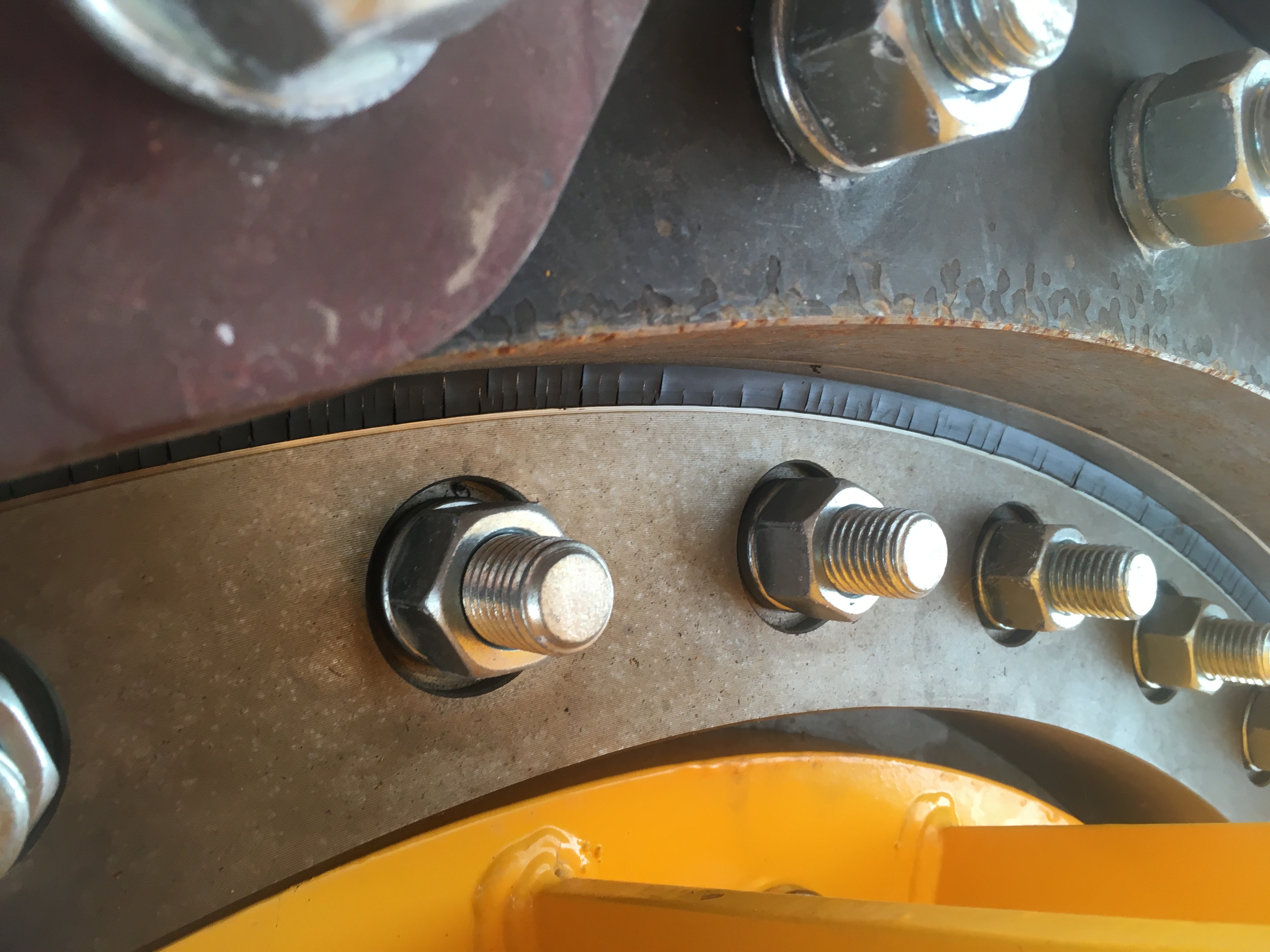
GREASE:
When we get calls regarding bearing failure, or warranty issues, 99% of the time it is attributed to a lack of re-greasing. Nothing screams bearing tightness and eventual failure like dirty, caky grease. Through regular use and outside contaminants, grease begins to break down. The seal on bearings is not hermetic, as it is only intended to keep large debris out of the raceway while keeping most of the grease in. Especiallyafter machines have been sitting idle during the Winter months, re-grease your bearing!
Old grease starts to get thick and dry, leading to bearing tightness, and in some cases, seizing. The balls in bearings don’t continuously rotate, as much of the movement is sliding, enabled by fresh, lubricating grease. Once the grease is past its serviceable life and the bearing tightens, turning torque rises steadily, increasing the load on your gearbox, motor, gears and pinions.
We recommend using most EP2 greases. Using the grease nipples provided on your bearing, pump new grease into the raceway until you start to see the old grease purge through the seal. While your bearing may have four or more grease ports, remember to rotate your bearing to ensure the grease reaches all areas of the raceway. We also recommend using gear grease on your gear teeth, should your bearing have them, while also removing any debris. These actions should be done at least every 100 hours of operation, with certain applications being able to go longer, and some needing re-greasing more often. Talk with a bearing supplier, or OEM, for more detailed information.
WHEN TO REPLACE:
While we expect most bearings to last at least 5-10 years, its not uncommon for us to get a call to replace a bearing that has been in use for over 20 years or more. The service cycle, loads, and load capacity all plays into this, but, regular maintenance and inspection will greatly increase your bearings’ life. When it is time to replace a bearing, there are a few apparent signs:
– Excessive Noise
– Material Flakes in the Grease
– Binding or Seizing
– Cracked or Broken Gears
– Noticeable Axial or Radial Play
If you have any of these issues, but are not sure it is time to replace your bearing, or you have any questions regarding regular maintenance, please contact Southern Sales & Engineering at 800.831.8377. Not only can we walk you through the inspection process, but we can provide more information on internal bearing clearances and testing procedures. With over 40 years’ experience in the bearing industry, and having been involved with countless different applications, we would appreciate any opportunity to share our knowledge. If a bearing is salvageable, we will let you know, as down time costs money. If it needs replacement, we are happy to work up a quick quote and delivery ISO Certified, high-quality bearings.